Three-dimensional scanning systems are becoming a new standard across all industries. The technology captures the shape of a physical object using a line of laser and produces data that can later be patched together and used for creating high-resolution 3D models.
Due to their widespread availability and ease of use, the market for 3D laser scanners is expected to grow at a CAGR of around 16.3% annually. Their value was estimated at $3.72 billion in 2020 and is projected to reach about $16.66 billion by 2030.
As 3D scanners help save time, cost, and effort, multiple industries apply this technology to their daily routine tasks. It works great for measuring and inspecting curved surfaces and complex geometries that require mountains of data for correct description. And their applications go far beyond the heavy industry. This report will bring you a few most common laser scanning trends across industries globally.
Architecture & Engineering
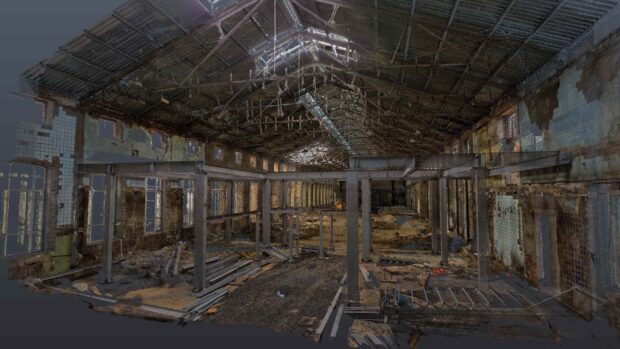
Architecture, Engineering, and Construction (AEC) is the largest industry in the global economy, accounting for 13% of the world’s GDP; yet, in the past decades, it has seen dismal performance. The reason is simple: construction projects are complex, and time and cost overruns have long become the norm. The 2020 National Construction Payment Report: Spring Spotlight on Jobsite Coordination shows that only 1 in 3 contractors (30%) finish projects on time and within budget. For 55% of construction businesses, it also means damages to their reputation.
Increased digitalization of the industry might help. In one study, 64% of architects report BIM has a high impact on improving the constructability of the final design, which can reduce or eliminate expensive rework in the field and improve cost and schedule performance. The information on the object is collected, processed, and designed to create a 3D model. The project stakeholders ensure the high quality and accuracy of measurements and can obtain access to a full report upon clicking on any element of this 3D model.
Using 3D laser scanners is a relatively new yet effective trend in the AEC industry. It supports open, transparent communication and a high degree of collaboration between stakeholders. Consider that a typical construction project accounts for 12% to 15% of rework; this percentage will go down to 1% or 3% using high-accuracy measurement technologies. On large construction projects running on tens of thousands of dollars of budget, such reduction eventually translates into savings and keeps the project on schedule.
Industrial Manufacturing
Industrial manufacturing has had similar issues to the AEC: long decision-making process, little transparency, and many mismeasurements disrupting the product design cycle prevent the industry from taking strides forward into the future.
Yet, Valuates Reports says it is all about to change as the industrial manufacturing segment will witness significant growth in the 3D scanner market share due to rapid use in three key areas:
- Product design: A 3D laser scan captures dimensional information of existing equipment, facility, or structure and generates a point cloud that later serves as a basis for product design.
- Development: The accuracy of 3D scans benefits reverse engineering for existing parts, saves cost, and shortens development cycles for machinery manufacturers.
- Product quality inspection: Thanks to the fast speed and precision of scanning technologies (high-end scanners measure 500K–2M points per second at 1 mm accuracy), a controller can determine whether products are made within specification thresholds.
Besides product design, terrestrial laser scans are actively used in the modernization of plants and factories. The device captures the spatial data inside and outside of the facility and creates a virtual representation of it in the form of a point cloud. Eventually, it becomes easier to check the built-in plant sections to be modernized or new machines to be introduced into the factory layout.
A study of 28 assembly plants in North America comprising billions of cubic square feet of manufacturing space reveals the key benefits of laser scanning tools. If an average cost to retool an assembly plant is approximately US$250 million, a 15% reduction in field change orders might equate to $3.5 million in savings in a single plant. In the words of Bill Campbell, an expert in 3D plant layout and 3D laser scanning, “It is not a question of if all major manufacturing companies will be using 3D laser scanning for as-built data collection and verification. It’s a question of when. The business case is undeniable.”
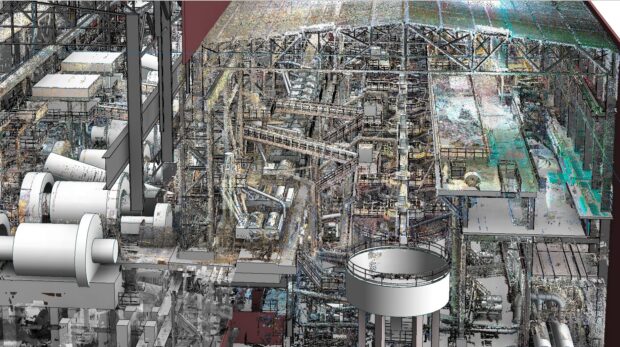
Aerospace & Defense (A&D)
In aerospace, even a slight defect or mismeasurement can put at risk the successful launch or mission of a space travel vehicle. An inaccuracy of just 1mm when assembling two prefabricated elements, especially on large objects, can result in massive deviations from their design intents. For this reason, aviation companies have the most strict requirements for quality and dimensional accuracy.
For this reason, digital thread and smart factory move into the mainstream of A&D company operating systems in 2022. Deloitte reports that at least 30% of the US manufacturers plan to implement digital thread initiatives, including digital twins and 3D prototyping. The role of laser scans in such use cases cannot be underestimated.
Using portable metrology equipment, like laser trackers or CMM arms, aerospace manufacturers can quickly inspect first articles, check pre-machined dimensions, and verify the quality of the part during the machining process. Engineers can identify hidden faults or malfunctions in aircraft components and diagnose them for further maintenance and repair.
3D laser scanners also enable the operators to carry out reverse engineering for obsolete, worn-out, or broken parts. When combined with additive manufacturing (aka 3D printing), non-contact laser scanners capture millions of data points and can help produce precision parts — from engine components to cockpit areas — while preventing the waste of material, budget, and time.
Automotive
The automobile industry follows a similar application of lasers as aerospace and defense. 3D scanning allows automakers to monitor vehicle components and ensure the correctness and precision of measurements in car parts.
In fact, the role of lasers is so important in the automotive industry and their benefits so vast that all BMW Group vehicle plants shall be digitalized using 3D laser scanning by 2023. Creating point clouds and BIM models, the company plans to merge the real and virtual worlds and virtualize car manufacturing in the hopes to implement new planning and remodeling of existing car parts in an efficient, precise, and flexible manner.
But there’s one aspect where automotive trumps all other industries in terms of the use of laser scanning: autonomous driving cars. Vehicles are equipped with special radars and LiDAR technology that detects objects surrounding the car.
Such use of laser technologies improves advanced drive-assisted systems (ADAS) and allows companies to keep up with government regulations. For instance, the European authorities have already put in place the Euro NCAP Advanced program providing guidance on the safety standards of self-driving cars. The bare minimum is blind-spot monitoring, Autonomous Emergency Braking (AEB), and vision enhancement.
A few examples of automotive companies that have taken great strides in the application of LiDAR and even won Euro NCAP Advanced Rewards are Volkswagen, Honda CR-V, the Mercedes-Benz G-Class, among others.
Out with the old, in with the new: Conclusion
Overall, recent advances in 3D scanning technology have the potential of enhancing — and even replacing — the existing system of measurements, adding more accuracy and optimizing speed on complex projects across industries.
It is only a matter of time until market players in construction, industrial manufacturing, A&D, and automotive, among others, will fully adopt the technology in their routine operations. The digital transformation of a business might seem scary at first; however, the vast number of benefits and cost savings yielded by 3D laser scanning might be a convincing factor in trying out the technology.